Bluing
Metal Polishing & Bluing
The key to an attractive metal finish lies in the preparation of the parts prior to finishing. At Sycamore Hill Designs, we can apply a bead-blast treatment for a matte finish, brushed-wire for a satin finish, and mirror polishing for a deep gloss finish.
1 of 8
Bluing
Metal Polishing & Bluing
Once the polishing is complete, the parts must be thoroughly cleaned, and all traces of oil and grease must be removed. Our Slow Rust Bluing process duplicates the antique method used for bluing firearms. Slow Rust Bluing is a time consuming, iterative process that requires repetitive treatment of the steel to form a layer of black iron oxide on the surface of the steel.
2 of 8
Bluing
Metal Polishing & Bluing
As the Slow Rust Bluing proceeds, the blue-black finish on the steel continues to darken and deepen. The final result is a metal finish that combines beauty with excellent durability and improved protection from corrosion.
3 of 8
Cold Case Hardening
Color Case Hardening is a heat-treating process originally intended to create a hardened steel part that would increase the part's durability. In a relatively narrow temperature band, this process will also produce some spectacular colors on the surface of the steel. Other shops will simulate the color case hardening process using chemicals or oxy-acetylene torches. At Sycamore Hill Designs, we use a true charcoal color case hardening process performed in a wood-fired furnace.
4 of 8
Cold Case Hardening
True color case hardening uses both bone & wood charcoal and, in a high temperature environment, combines these materials with the parts to be hardened. The bone & wood charcoal mixture is prepared in steel crucibles where the parts to be treated will be loaded.
5 of 8
Cold Case Hardening
The polished & prepared steel parts are loaded into the crucible along with the charcoal mixture. The parts are completely covered with the charcoal, and the crucible is sealed and loaded into the furnace.
6 of 8
Cold Case Hardening
The crucible containing the parts for color case hardening are placed in the furnace, and heated to the appropriate temperature band. The combination of heat and nitrogen from the bone charcoal creates the random color patterns on the surface of the steel parts. Carbon from the charcoal penetrates the surface of the steel to create a hardened "case" on the part.
7 of 8
Cold Case Hardening
After a period of time at the correct temperature, the crucible is removed from the furnace, and the parts are "quenched" - cooled quickly - to retain the colors and hardness introduced in the heat treating process.
The finished parts show the reds, blues, and gold colors characteristic of this heat treating process.
8 of 8
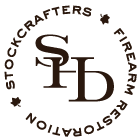